Unleashing reliability: Overcoming power challenges with transformer condition monitoring and the journey to 100% uptime
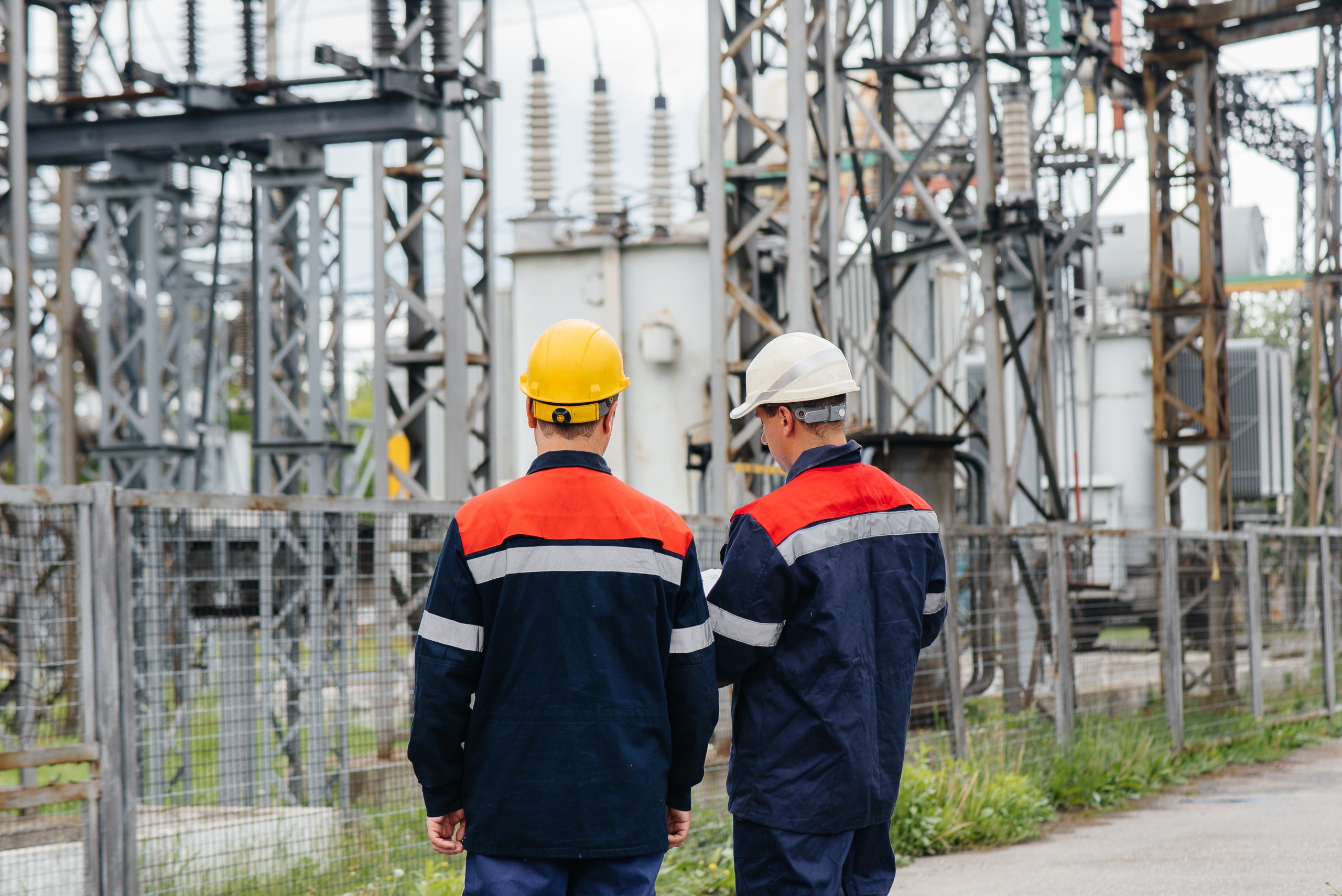
In today’s rapidly evolving asset management arena, achieving 100% uptime for critical systems is no longer an unattainable dream but an essential and formidable challenge, especially in regions grappling with adverse infrastructure conditions. In South Africa, engineering managers face the daunting task of maintaining an uninterrupted power supply amidst unreliable infrastructure and frequent power outages. As we build upon our previous article discussing the quest for uptime with switchgear, we now focus on the indispensable role of transformer technologies in delivering stable and efficient power to critical loads. This article will explore the importance of condition monitoring technologies for transformers and how they stand as stalwarts in achieving the elusive 100% uptime. From embracing smart transformers to harnessing advanced predictive maintenance tools, we will delve into the latest trends and best practices in transformer technology. We aim to equip engineering managers with invaluable insights to overcome challenges, stay ahead of the curve, and ensure relentless power reliability in the face of ever-changing conditions.
The evolution of transformer technologies
Over the years, transformers have profoundly evolved from traditional static devices to intelligent, connected assets. The advent of smart transformers has been a game-changer in the power industry by incorporating digital intelligence, enabling intime monitoring, analysis, and control. These smart transformers offer remote monitoring, diagnostics, load management, and other capabilities. Communicating and exchanging data with the grid optimises energy distribution, mitigates faults, and enhances overall system reliability.
The significance of remote monitoring in transformer health
Due to the high cost of replacement, removal from service and repair, remote monitoring has emerged as a cornerstone technology towards achieving 100% uptime with transformers. This approach entails the utilisation of sensors, data analysers, and IoT devices to continuously monitor crucial parameters such as temperature, current, voltage, online partial discharge, dissolved gases and dielectric condition. With intime data collection and analysis, valuable insights are gained into the transformer’s health and performance, allowing prompt detection of anomalies and potential issues. By taking proactive measures through remote monitoring, unplanned downtime can be minimised, and critical systems can be kept operational and reliable.
Leveraging predictive maintenance with data analytics and machine learning
Predictive maintenance strategies have fundamentally altered the management of transformers. We can anticipate potential failures and implement timely maintenance actions by harnessing the power of data analytics, machine learning algorithms, and historical performance data. This approach minimises downtime and extends the equipment’s lifespan, leading to significant cost savings and reduced risk associated with unexpected breakdowns. Predictive maintenance ensures that maintenance efforts are targeted and efficient, maximising transformer uptime, maintenance costs and performance.
Four fundamental condition monitoring technologies for transformers
- Dissolved gas analysis (DGA): DGA is a powerful technique to detect and diagnose potential faults within transformers. DGA is a degenerative condition which can provide critical information about incipient faults such as overheating, arcing, and insulation degradation by analysing the gases dissolved in transformer oil. Early detection through DGA allows timely maintenance to be planned proactively, preventing catastrophic failures and ensuring the longevity of the transformer.
- Partial discharge (PD) monitoring: PD monitoring is an effective method for assessing the condition of transformer insulation. PD events are precursor indicators of insulation degradation and can lead to catastrophic failures if left unaddressed. By deploying in tank and bushing PD monitoring systems, PD activity can be detected, monitored and analysed, allowing corrective actions before significant damage occurs.
- Bushing monitoring: Transformer bushings are vital components that connect the transformer windings to the external network. Monitoring the bushings can help identify issues such as degenerative conditions and insulation breakdown, impacting the transformer’s performance and reliability.
- Temperature and hot spot monitoring: Continuous temperature monitoring of critical transformer components, including windings and core, is crucial for early detection of overheating, overloading and insufficient cooling. With an early warning of temperature rise and increased loading, additional cooling being implemented can increase the transformer’s return on investment by reducing the thermal stress placed on the paper insulation system. Engineering managers can set preventive measures to avoid thermal stress and potential failures by monitoring temperature trends and selecting additional cooling earlier to reduce oil/paper insulation system stress.
What risks can remote monitoring avert at a power plant?
By employing remote monitoring technologies, we gain valuable insights into the transformer’s health and performance, mitigating various risks that could compromise the plant’s operations. For instance, temperature sensors are instrumental in detecting hot spots (especially under adverse conditions) within the transformer, which may indicate issues like insulation degradation, overloading, thermal faults, or the collapse of the dielectric fluid. Early detection of these condition-related attributes enables engineers to take engineered decisions and prompt action, such as implementing additional cooling measures, adjusting loading, or evaluating distribution parameters. These measures will prevent further damage and ensure uninterrupted operation. Additionally, remote monitoring through moisture, dielectric strength, gassing and oil condition helps detect a deteriorating internal environment within the transformer. Such anomalies may signal loose connections, winding issues, or impending insulation failures. Timely detection of these issues allows for proactive maintenance, reducing the risk of transformer failures, electrical faults, and unplanned downtime.
With condition monitoring technologies in place, power plant operators can ensure the longevity and reliability of their transformers, enhancing overall power system resilience and minimising potential disruptions.
Staying ahead of the pack
Engineering managers must continuously embrace innovations and best practices towards achieving 100% uptime and staying ahead of the competition. Incorporating redundancy and backup systems, implementing comprehensive testing and training programmes, and adopting cutting-edge condition monitoring technologies are essential to ensuring critical systems remain operational, even in challenging conditions. Staying updated with the latest advancements in transformer technology enables optimised performance, reduced operating costs, and a competitive edge in the industry.
The importance of condition monitoring technologies for transformers cannot be emphasised enough. With the integration of smart transformers, remote monitoring, and advanced predictive maintenance tools, achieving 100% uptime is within reach. The proactive condition monitoring approach ensures critical systems’ smooth and reliable operation and offers significant cost savings and reduced risk of repairs and unplanned downtime. By staying ahead of the curve and leveraging the best condition monitoring technologies, engineering managers can achieve their goal of 100% uptime, securing the success and sustainability of their operations in today’s dynamic power landscape.
Read more about our intime monitoring and analysis service solutions for transformers here.