Condition Monitoring Reliability Advisory Services
To run an effective reliability programme that maintains a safe and risk-free environment, while attaining the full useful life of plant equipment, you need a clear understanding of the effectiveness of your condition monitoring programme.
This is the one area where the use of specialist consultants can add significant value as their objective view, and broad sector experience can help identify gaps caused by the lack of, or poorly applied condition monitoring tools and tactics. Their extensive experience can also help prioritise corrective actions to ensure quick wins with long term rewards.
Martec advisors integrate engineering fundamentals, technologies (including IIoT), workflow processes and resource management when they help clients to assess the status of their condition monitoring programme. With the client’s participation and input, the development, rollout and execution of a custom reliability programme (fit for purpose with a range of CM tools), are firmly managed by predetermined key performance indicators (KPI’s).
Range of Advisory Services
Defect elimination, Failure investigation and Root Cause Analysis
Assist the plant owner to find the root cause of failures and prevent a recurrence.
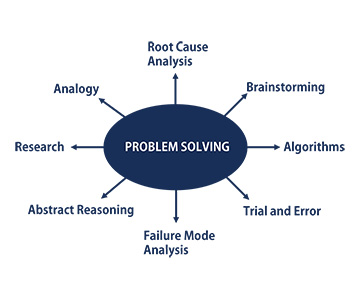
Witnessing factory acceptance tests
Act as an independent third-party witness, verifying design and repair to specification.
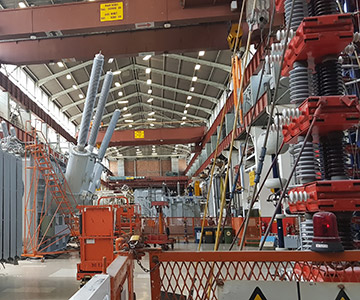
Operational readiness evaluations and baseline assessments
Perform design reviews and evaluate plant readiness. Conduct baseline condition assessments to identify latent and design defects.
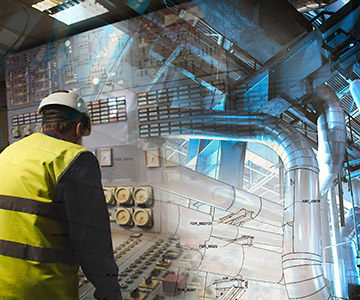
Consulting
Helping clients with specific focused improvement projects to improve the reliability of their mechanical and electrical plants.
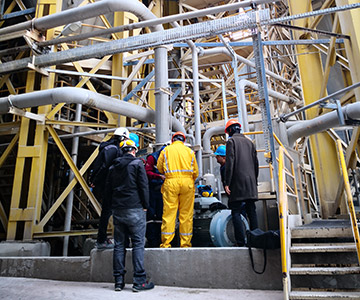
Condition Monitoring Improvement Programme (CMIP)
Assessing Condition Monitoring practices and developing an improvement programme that will deliver improved plant reliability.
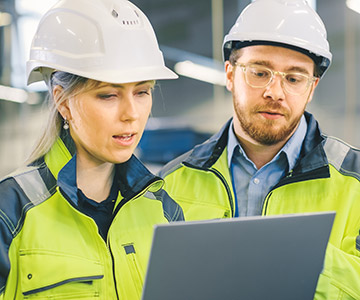
Condition Monitoring Improvement Plan
Many companies simply run condition monitoring programmes without a defined ideal state. One way to achieve a clear understanding of the status of your condition monitoring programme, measured against such an ideal state, is by conducting a condition monitoring maturity assessment.
Martec’s advisors will use their condition monitoring improvement plan to help you define your ideal state and identify shortfalls and set priorities to bridge the gaps to ensure that your reliability capabilities, performance and resources are aligned to deliver on your condition monitoring strategy.
How it works
A structured six-step approach is followed to work through all aspects of a comprehensive condition monitoring programme based on ISO 17359.
The assessment consists of 10 key performance areas (KPA), each with three to seven associated key performance indicators (KPI). These KPIs are measured against a maturity scale with the lowest maturity at one (firefighting mode) and the highest maturity at five (excellence).
Several structured interviews with engineering and maintenance staff and visual plant inspections are conducted to gather assessment data. Historical and present data is also utilised for comparison to similar machines in the industry. Martec’s consultants analyse the data and provide a detailed report with useful information pertaining to gaps identified and corrective actions required to improve the condition monitoring programme to the desired state.
A client then has the option to further contract with Martec’s advisors to develop a condition monitoring strategy and to roll out the agreed condition monitoring programme.

Do you really know the real condition of your plant equipment and how close you are to a catastrophic event?