Ensuring resilience: Navigating transformer risks through advanced monitoring and IoT implementation
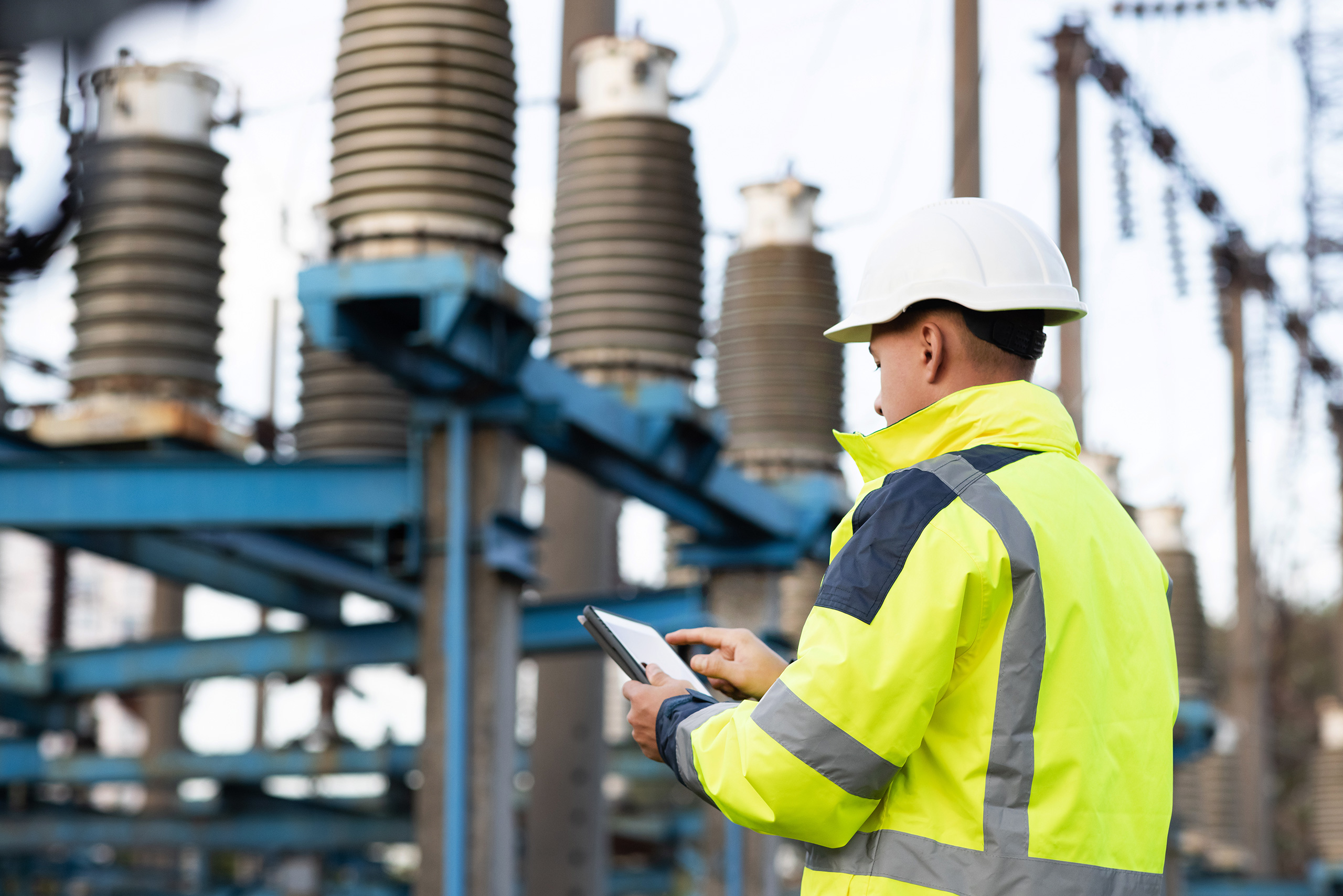
Embracing innovation in transformer management
Critical infrastructure management has leapt forward in an era dominated by technological advancement – and transformers are no exception. Gone are the days of relying solely on reactive maintenance, as integrating risk assessments, online monitoring, and the Internet of Things (IoT) promises a new dawn for transformer management. As we delve into the intricate world of transformers, we uncover the pivotal importance of tracking asset and condition risk, shedding light on achieving the elusive goal of 100% uptime.
I. The dual frontier: Asset risk and condition risk
Navigating the terrain of transformer management requires addressing two distinct yet interconnected facets: asset risk and condition risk.
Asset risk
Transformers represent substantial investments in any power infrastructure. Ensuring their longevity and optimal performance is paramount. Asset risk encompasses the probability of:
- a safety incident occurring (if power is lost for more than 24 hours)
- associated financial loss
- environmental risk
- contingency design (N minus 1 contingency and alternative back feed options)
- strategic spare unit availability
- repair capability and time frame
- a transformer’s lifespan, considering age, design, and maintainability factors.
In this context, asset risk refers to the potential financial jeopardy from the loss of power to critical plant and is tied to the entire lifecycle of a transformer. This evaluation considers the transformer’s age, design intricacies, substation design and network interconnectivity. Practical asset risk assessment involves meticulously analysing historical data to discern network performance patterns or susceptibility to faults affecting the transformer and the equipment it supplies. In essence, it is the examination of the unavailability of that power source and the consequences of the absence of the power source.
Condition risk
Condition risk focuses on the internal health of transformers in the short- medium- and long-term. Oil-filled transformers are very forgiving and can operate under severe neglect. Neglected and often overlooked maintenance practices lead to costly breakdowns and lengthy service interruptions or repairs that require the transformer to be removed from service and shipped to a repair facility. Frequently, the shipping cost alone is very costly. It is when the transformer has been neglected that unexpected failures occur. These instances can lead to dire consequences, such as fires and the destruction of other equipment!
In the operation of these transformers, some condition parameters take many years to manifest or become apparent. Some take several months to change, and others mere minutes or seconds to occur. The latter set of condition parameters are the parameters every transformer operator or owner needs to monitor more intensely. Traditionally, a transformer’s “lifeblood” (aka oil or insulating fluid) is used to detect these condition changes.
Focusing on the more short-term condition is the breakdown of the fluid into gases that can be extracted from a transformer’s fluid body and chemically analysed. These gases can show several other conditions with different interpretation tools (eg Duval triangle, Duval pentagram, gas ratios). These parameters are often used as a gauge for the internal condition of the transformer. However, a thermometer only tells one what the temperature is and, in essence, cannot tell what the illness is. The use of computer databases can assist in extracting the correct data and forming a picture of the transformer’s health.
Considering the above, it is necessary to understand that there is a process of acquiring the data from the analysis. This process is often flawed and takes up to two months to obtain.
Enter the realm of online monitoring – an innovation that is pivotal in transformer management. By deploying online devices such as online DGA (dissolved gas analysis), dielectric, bushing and tap-changer monitors and harnessing the power of data analytics, online monitoring unveils a faster cycle into the transformer’s inner workings. For instance, a sudden spike in the gases beyond established thresholds could indicate a partial discharge, arcing or overheating issues, or a dip in oil quality might hint at an element of neglect and have a long-term impact on insulation degradation. From a bushing monitoring aspect, a shift in the tan delta measurements could show that a bushing is about to fail. A tap changer monitor can highlight added stress on the on-load switching device and cause premature failure. Additionally, oil quality irregularities could point towards loss of insulation capability and longer-term damage to the paper insulation, impairing the transformer’s ability to withstand the network variations and through fault instances. The value of this approach lies in its proactive nature.
Detecting these anomalies at their developing stage empowers utilities to initiate targeted interventions, preventing the domino effect of catastrophic failures and fortifying the overall robustness of the system against unexpected adversities. Higher instances of network disturbances such as cable theft, loadshedding, short circuits and overloading all affect the transformer’s reliability.
II. The digital vanguard: Online monitoring and IoT implementation
Online monitoring
Online devices strategically placed within a power delivery system network relay vital data to central control centres, where advanced algorithms decipher the information, enabling better predictive maintenance and swifter response to deviations from the norm. This intime vigilance transforms risk management from a guessing game into an informative science and resilient supply network.
These online devices meticulously collect a wealth of critical data, ranging from moisture-in-oil and temperature variations to dissolved gas composition nuances and bushing condition intricacies. This wealth of information embarks on a swift and seamless journey from devices to cloud-based applications to dashboards. It has algorithms to decipher the incoming data, unveiling patterns hidden from the naked eye. Enabling enhanced engineering decisions to safeguard the operations under normal and adverse operating conditions when needed, thus delivering the best short- and long-term performance.
Let’s step into a real-world scenario within a plant where the delivery of electrical power is vital. A transformer monitored by its intricate set of devices is available and able to supply the demand needed to ensure the plant delivers. On a typical busy day, soaring electricity demand prompts devices to detect and flag abnormal strain on components, signalling a potential power failure. Swiftly, crucial data is sent to a cloud-based dashboard, where advanced algorithms promptly identify an anomaly and track development. Production is critical, and power loss to the plant would be detrimental to the output of the plant. The proactive response isn’t just immediate; it’s part of predictive maintenance, leveraging data mining of historical and intime data to anticipate issues. Having both the network, asset and condition risk at hand enhances the ability to shift power flow from one network to another or an alternative supply.
What was once a guessing game, where maintenance decisions were based on a mix of historical practices and intuition, has now transmuted into an engineered solution. With its synergy of monitors, data analytics, and predictive algorithms, online monitoring can breathe life into proactive risk management.
Holistically, the risk model and the data associated with the risk data assist in forming a picture of where to spend the maintenance budget wisely, thus getting the best reliability from the power plant assets employed. Ultimately getting both performance when needed and return on investment optimised.
IoT Implementation
Before venturing into an extensive solution, it is best to consider the transformer’s network and the equipment it supplies power to. Much of the decision will be based on the importance of the equipment or processes provided by that transformer. As an example, consider a transformer that supplies power to a furnace. If the power transformer feeding that furnace were to stop functioning, the processes reliant on that hot metal would be without material to produce the end product. Again, in a different context, if the transformer supplied power to 200,000 households or businesses, those households and businesses would cease to function normally, plus the associated loss of revenue. Generally, the operation of the transformer in its environment and supplied load (typically the processes or customers) needs to be the focus of the asset risk. Setting up the correct asset risk evaluation is invaluable in understanding which asset needs to be monitored closely and more frequently.
Once the asset risk is determined, the condition risk can be used as a final step in the process. Taking the assets with the highest asset risk and using the condition risk to tweak the list to indicate which assets deserve closer scrutiny and enhanced monitoring. The asset highlighted in the analysis would be the best candidate to apply the IoT technology.
With the appropriate monitors, these transformers can provide reliable data that can be sent to the decision-making engineers, sharing intricate insights about the transformer’s health. For example, a transformer detects a surge in demand as factories ramp up production during the day. This information is published to a dashboard, allowing Operations to proceed with the comfort of knowing the power delivery system is stable and they can see the production run to its completion.
III. Pinnacle of reliability
The pursuit of perfection
The quest for 100% uptime may sound utopian. However, with IoT implementation, utilities can proactively address potential issues before they snowball into crises by having the details of network- and asset risk combined with sound condition data, allowing the system to operate at its peak. Predictive maintenance, guided by data-driven insights, minimises downtime and maximises efficiency.
Synergy in action
The synergy between asset risk evaluation and condition risk monitoring is the cornerstone of continuous power. As plant owners refine their risk assessment strategies, they align maintenance schedules with intime condition updates, ensuring that transformers are optimised for performance throughout their lifecycle.
Illuminating the future of transformer management
The combined force of network risk assessments, online monitoring, and IoT implementation to communicate the data is revolutionising transformer management. The importance of tracking assets and their condition risks cannot be overstated. The amalgamation of these cutting-edge technologies enables transformer owners to proactively safeguard transformers, minimising disruptions and inching closer to the coveted 100% uptime.
To read more about our transformer monitoring services, click here.